蒸気洗浄機の製作過程をできる限り公開します!0から洗浄機ができるまでをご紹介します!部品洗浄でお困りの方、ご一報お待ちしております!
皆様お世話になっております。本日から10月がスタートしましたね。10月といえばインボイスですね。弊社でも今月からインボイスを発行していきますので今後ともよろしくお願いします。
さて、今回はいよいよ弊社の主力となっている蒸気洗浄機の製作過程をまとめていきたいと思います。この搬入時期は1月になりますので、先週から組立を始めております。
さすがに、事細かにはできませんが皆様への情報提供の一つとして綴っていきたいと思います。アイキャッチは最後の完成形をのせたいのでそれまではどうするか考え中です。
架台フレームの組立
まずはやはり土台回りのフレームから組み立てていきます。フレームは例によってユキ技研さんの「レコフレーム40シリーズ」を使用します。
もう既に前面にIAIのロボシリンダが乗せられていますね。
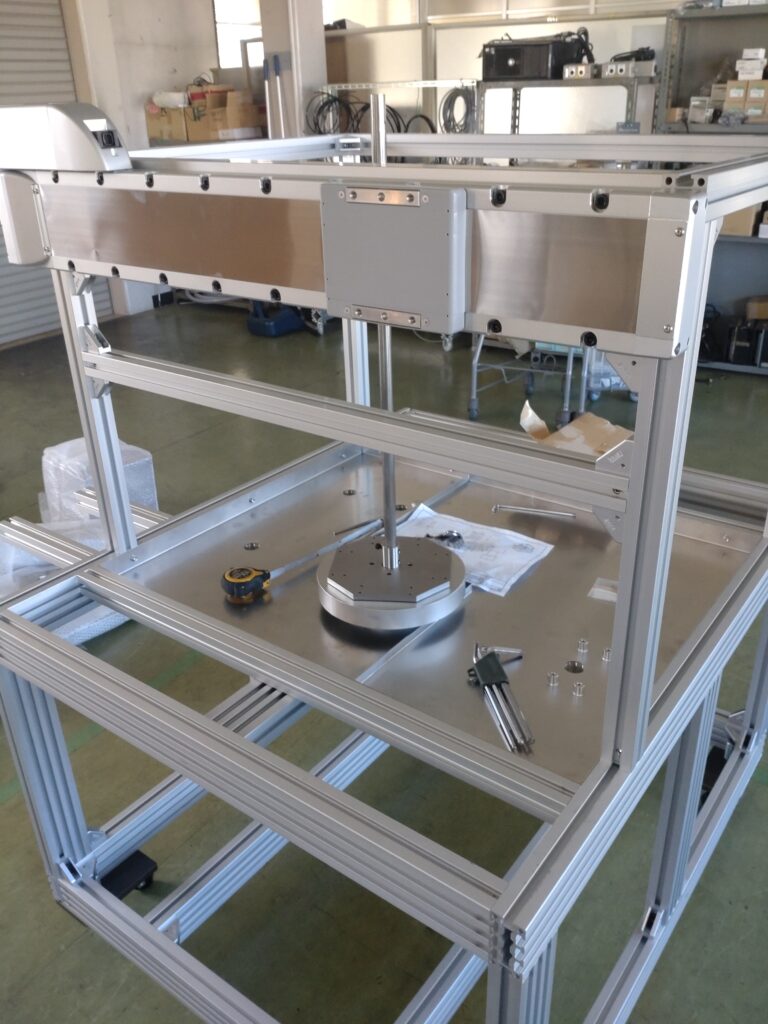
材料が・・・たくさん・・・
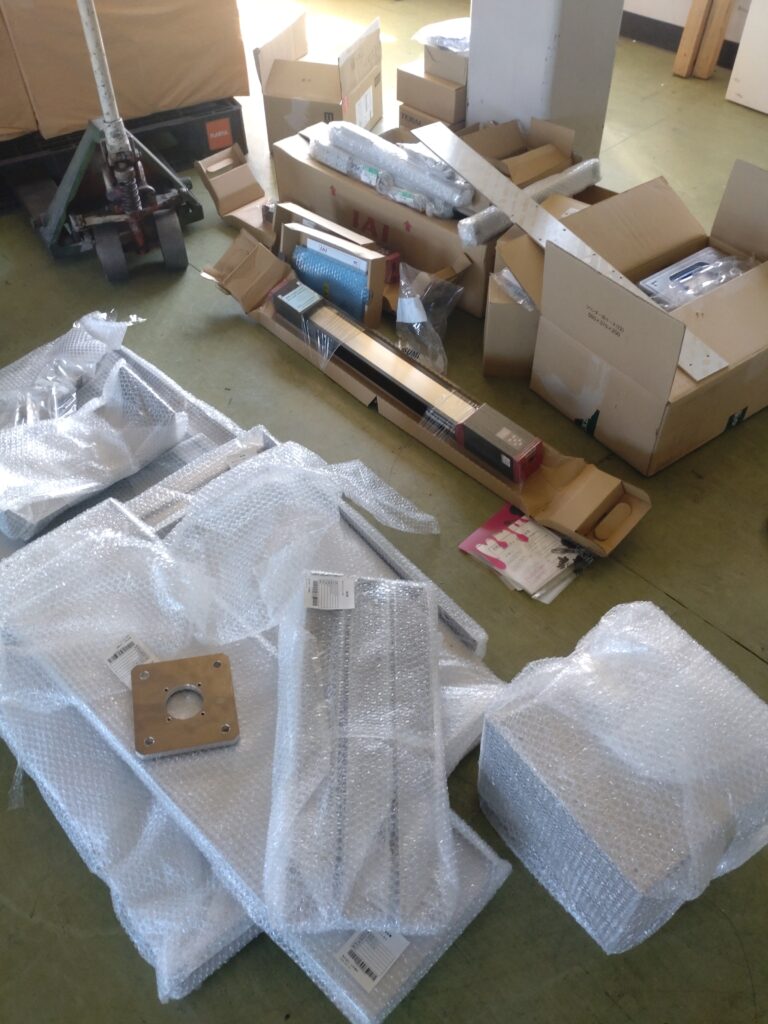
本体部カバー、Z軸、ハンドの取付
側面、背面のカバーがつき、それらしくなってきましたね。Z軸はIAIのエレシリンダーを使用しました。
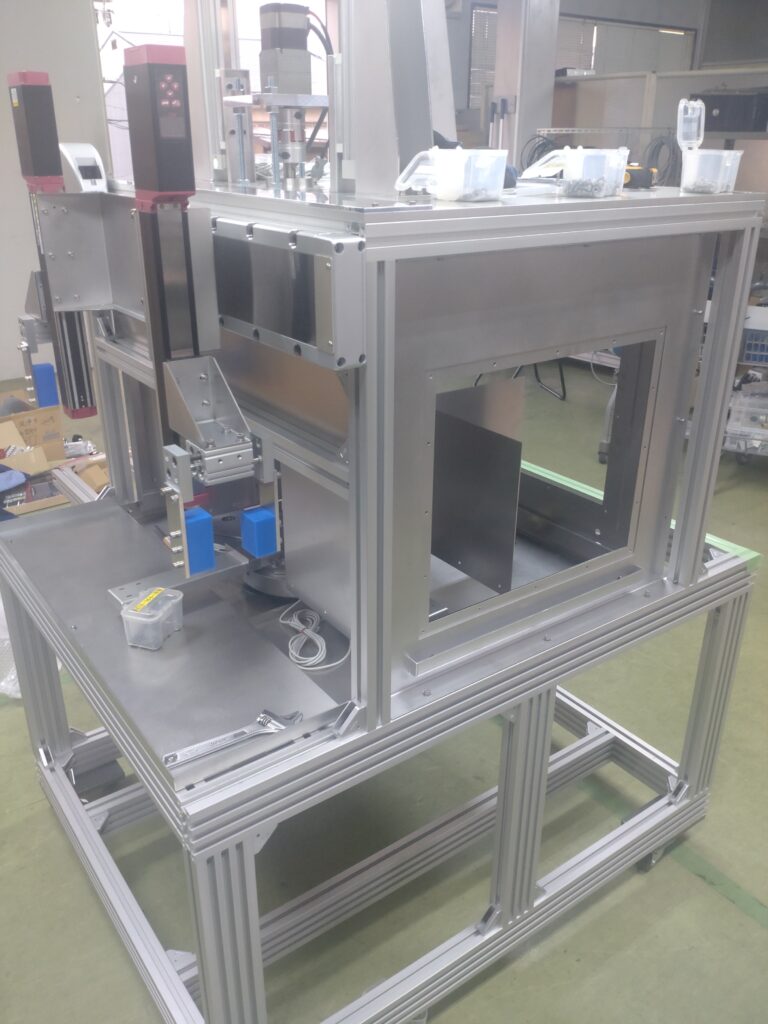
後ろからみた感じです。窓をあけて作業をしておりましたので蚊よけのために「蚊取り線香」をつけてます。エアコンは節電のためできるだけひかえています。
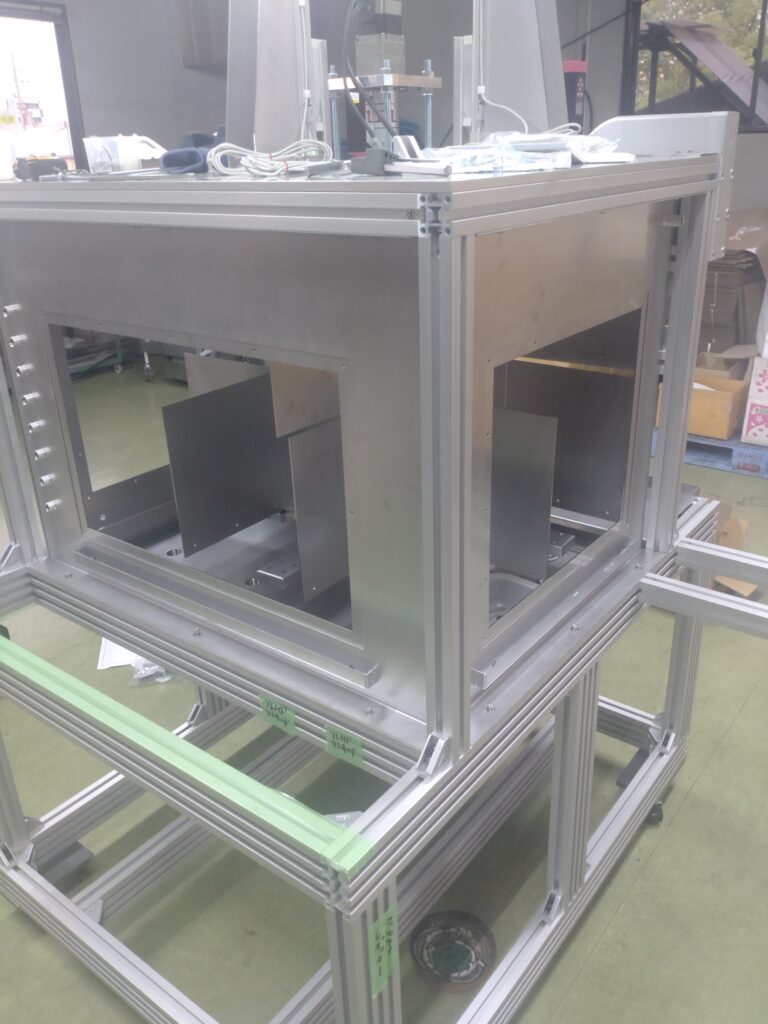
配線作業にはいります。
11月15日、いよいよ配線作業に入りました。制御盤と機械配線はいつもお世話になっている電機屋さんにお願いします。中小企業は常に横のつながりを大切にしながら仕事を進めていく必要があります。その他にも組立のキャパが超えそうな時はメカ屋さんに協力していただくこともあります。
今回の電動は、横軸はロボシリンダ、縦軸はエレシリンダを採用しております。
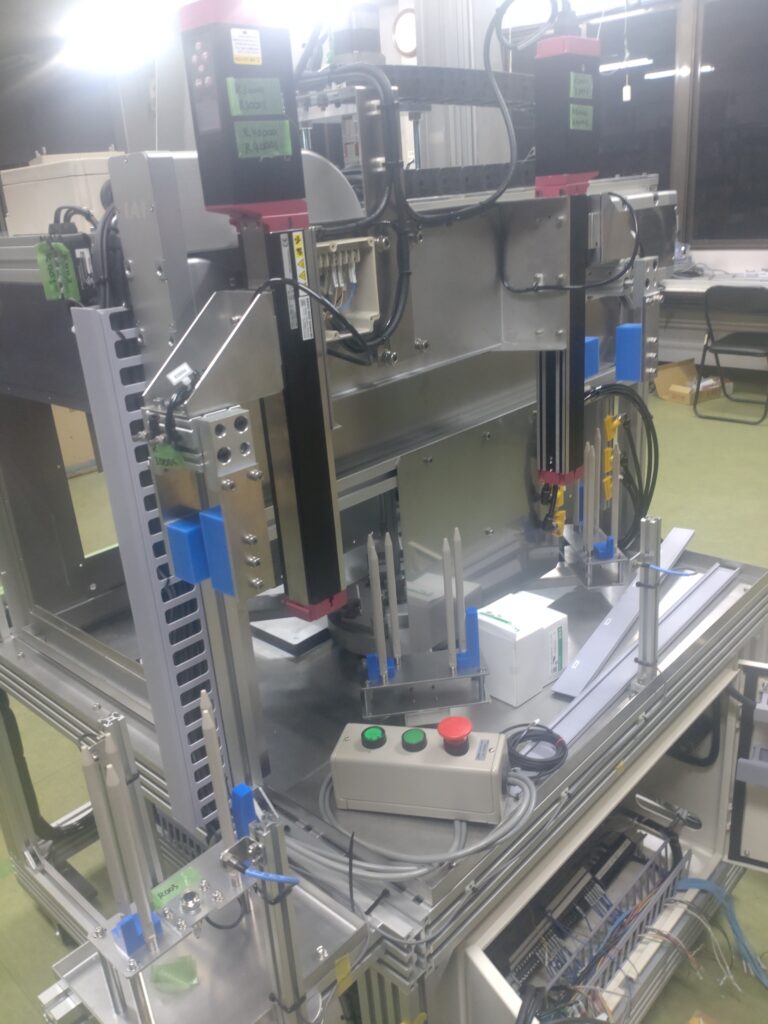
ソレノイドバルブも配線が完了しました。エア配管はこれからやっていきます。シリンダからの取り回しを考えてキレイにしていきたいと思います。
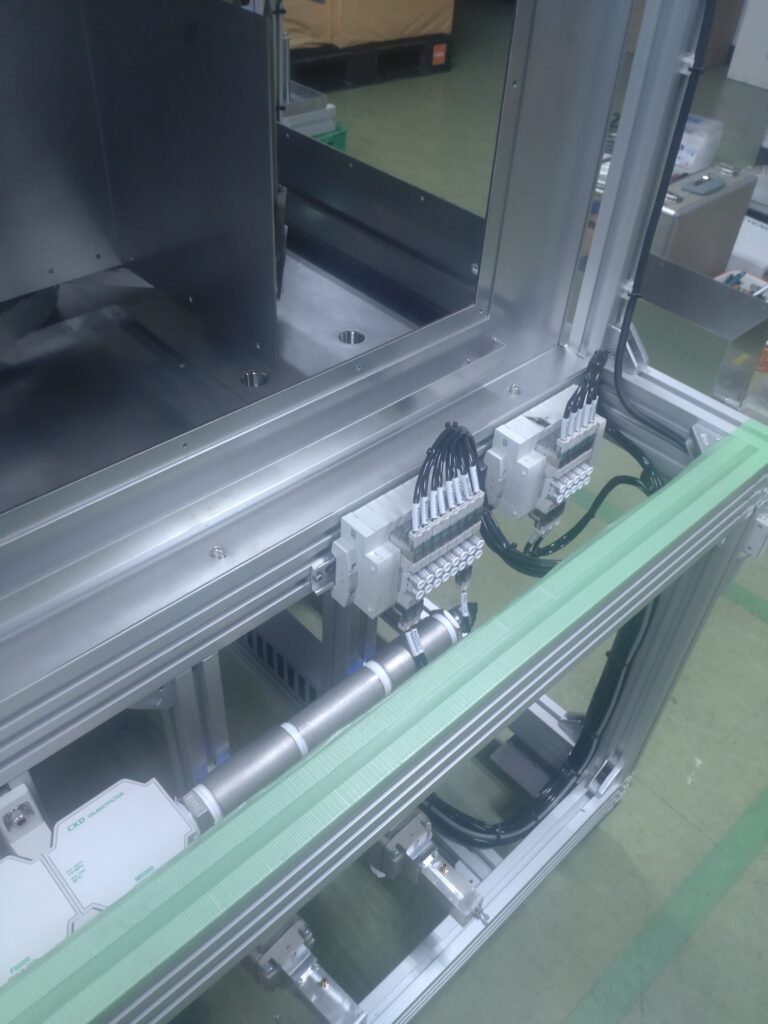
まだまだ先は遠いです。
本体装置のとなりに配置するオプション設備の組立をしてます。今回の洗浄機についてはZ軸は全てアイエイアイのエレシリンダを使用することにしました。理由としてはもろもろありますが、搬入する工場内の環境が切削油がミスト上になっている場所であったり、埃や油の付着が多いことからソレノイドバルブの故障リスクを軽減させれるのではないか?と思い採用しています。またエアー機器を減らすことで省エネにつながることが利点でもあります。
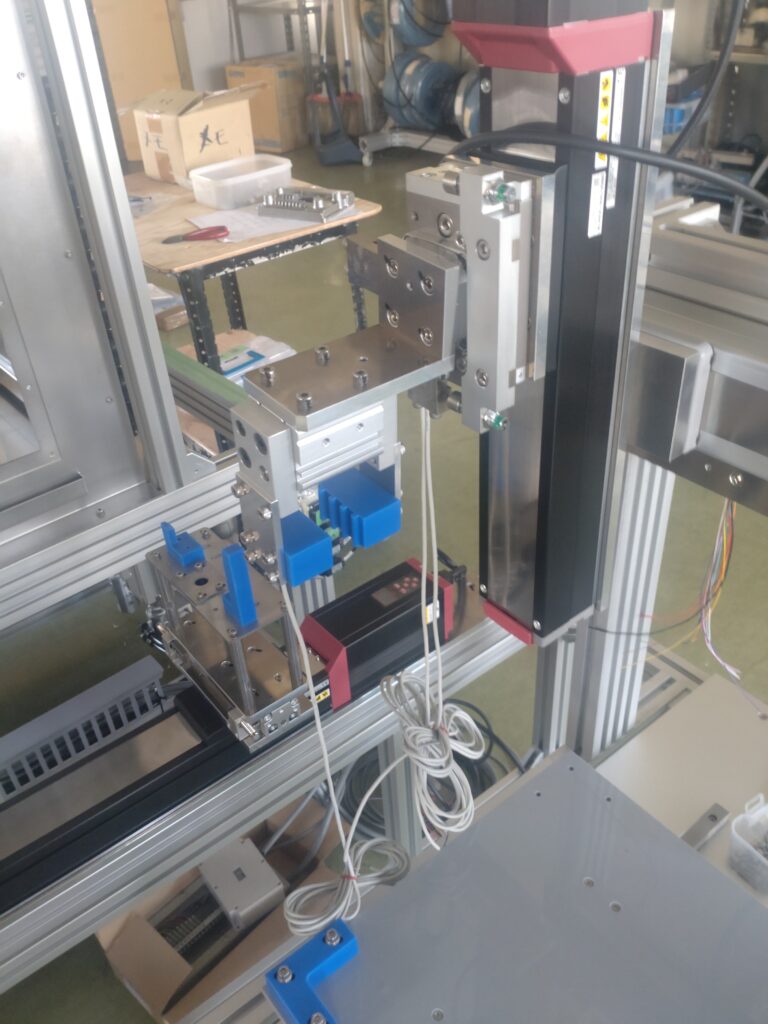
製品パレットをのせるベースです。材質は塩ビを使っています。四隅のコーナー(MCナイロン)で箱の位置決めをし、自動でワークを箱の中に挿入していく構造です。
パレットはピッチ送り動かすのでロボシリンダを使用します。
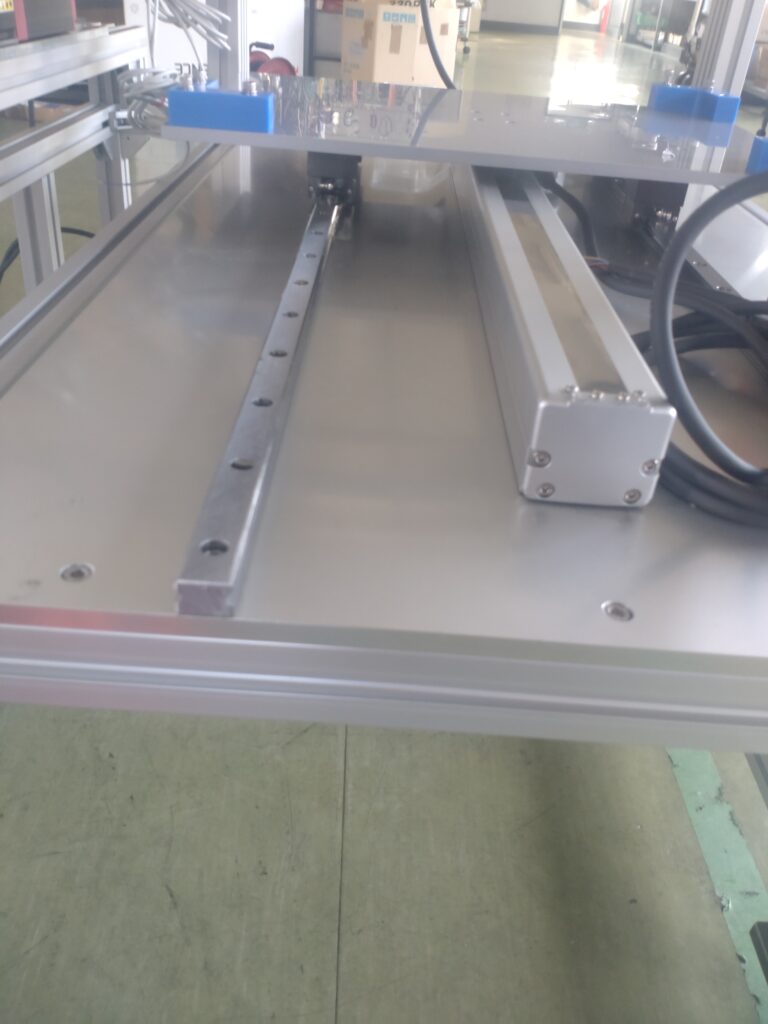
本体背面のエア配管も順調に進んできました。左の黒のエアチューブφ10はエアブロー用に洗浄機内に接続します。コンプレッサーエアーは油分が含まれますのでフィルター、オイルミストフィルターにてできる限り除去する配管構造にしています。
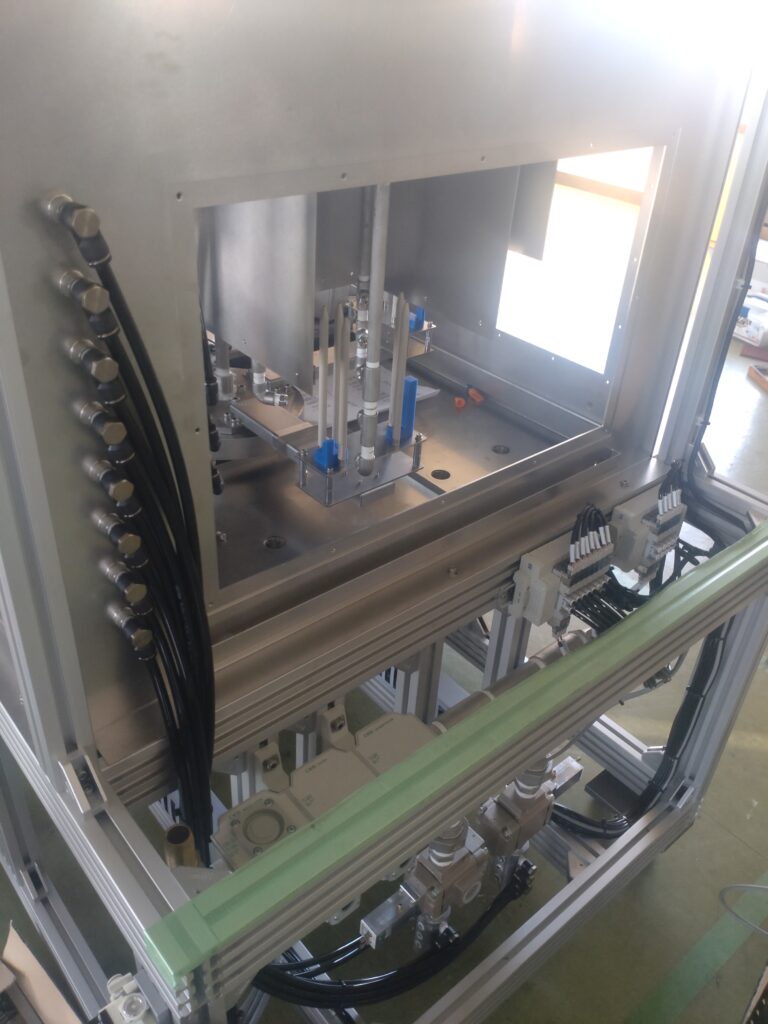
まだ、先は遠い。
12月16日、組立ペースをどんどん上げていきましたので、カタチになってきました。事前にはラダー図もたたき台を作っていますので試運転できる日も近づいてきました。
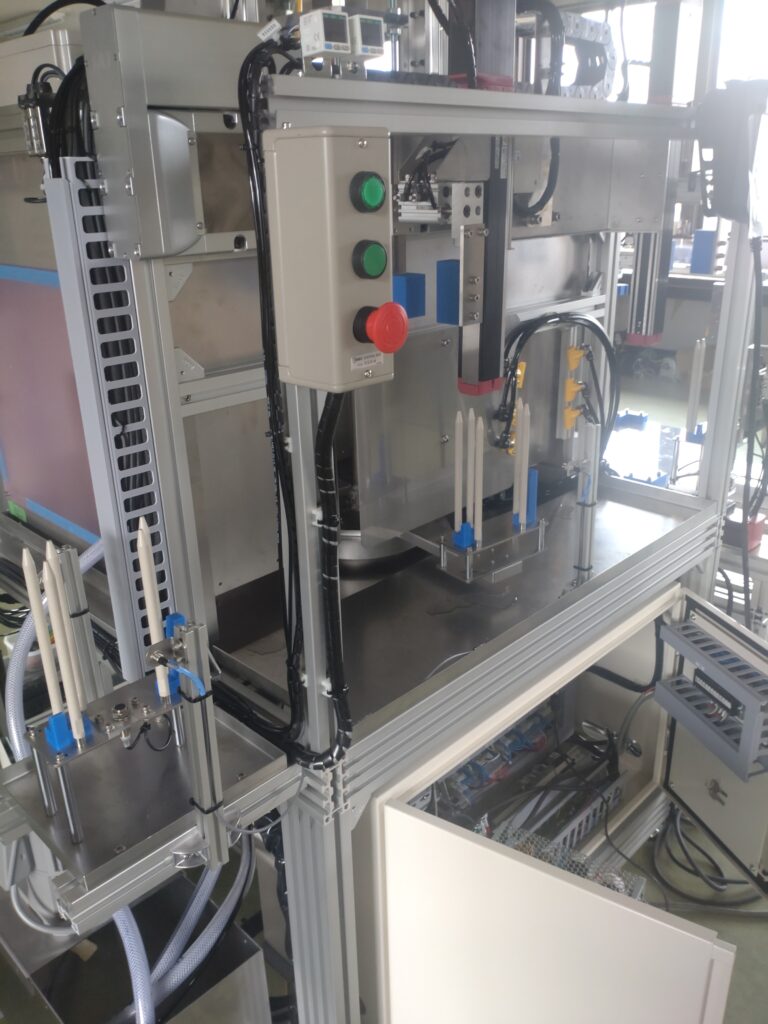
全体としてまとまってきた感じです。組立に問題はありませんが、一番心配なのは「水漏れ」とワークへの「水残り」です。早く試運転をかけてそれらをチェックしていきたいです。
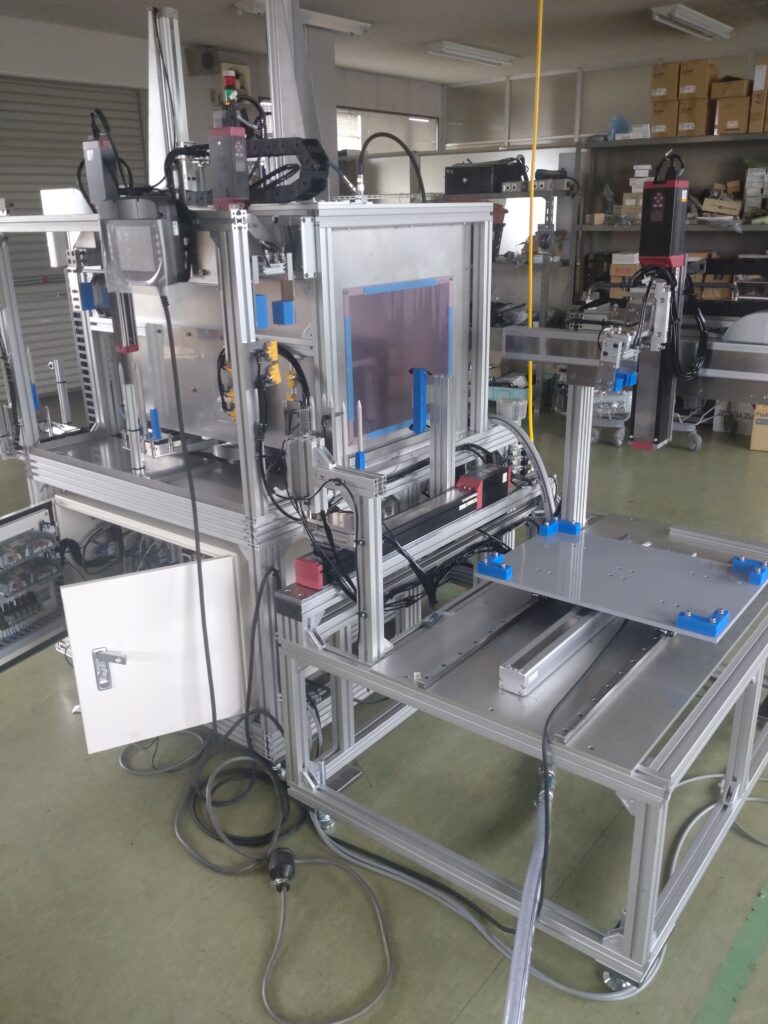